
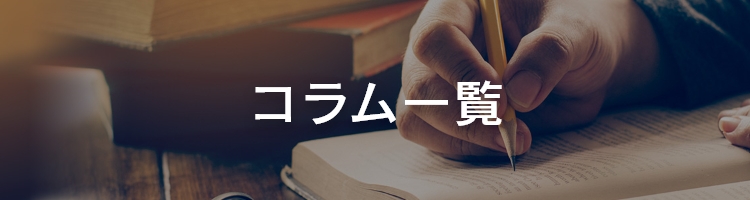
食品製造業が行うべき5S活動とその効果について
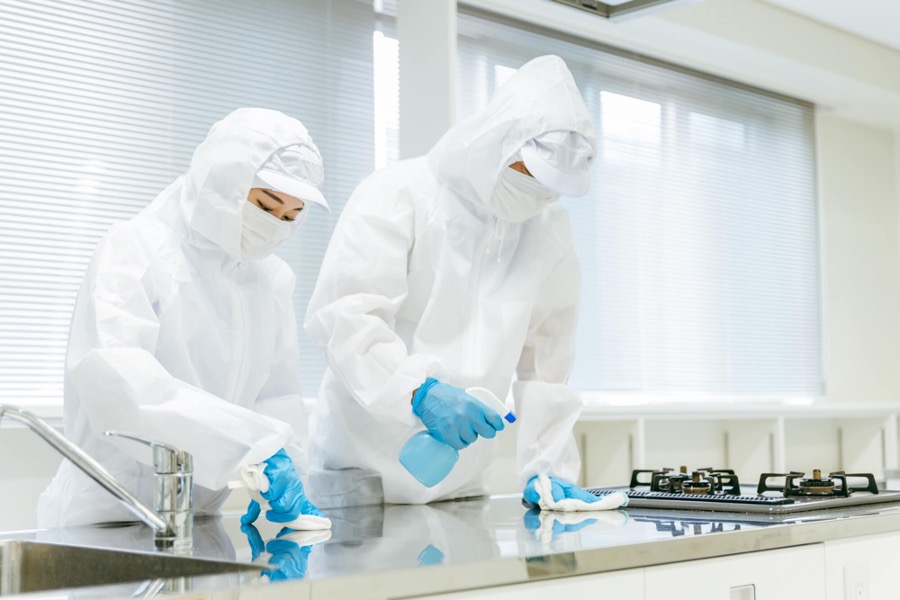
食品製造業であれば知っていて当たり前とも言われる「5S活動」。しかし、その意義や重要性、実施時のポイントについては、言葉の認知度を超えることはありません。そこで今回は、食品製造業が行うべき5S活動について、詳しく解説します。
食品製造業が行うべき生産性向上
まずは前提として、食品製造業の生産性向上について認識を合わせておきましょう。
生産性とは、投入される生産要素(労働、設備費、原材料費など)に対する産出物の割合のことです。簡潔に表すなら、少ないリソースでより多くの製品を生産することで、生産性は向上します。
生産性の向上は利益の増大、コスト削減、品質保証などにつながります。つまり生産性が高ければ多くの製品を製造・販売でき、不要なコストを減少させ、一定の品質を維持できるようになるのです。
生産性向上のポイント4つ
食品製造業において、生産性を向上させる基本方針としては、以下の4つが挙げられています。
5Sによる効率化
整理、整頓、清掃、清潔、しつけを通じて、無駄な手間を削減し、生産効率を向上させます。
ボトルネック工程の改善
生産ラインで時間がかかる部分や効率の悪い部分を特定し、その問題を解消して生産全体のスムーズさを向上させます。
レイアウトの最適化
製品や作業工程に応じた最適なレイアウトを設計し、無駄な移動やリードタイムを削減します。
自動化・無人化
ロボットや自動設備の導入で、時間がかかる作業や人のミスによる不良を減少させ、生産性を大きく向上させます。
5S活動とは?
ここからは、前項でご紹介したうちの、5Sによる効率化について詳しく解説をしていきます。
5Sは、整理・整頓・清掃・清潔・しつけの5つの要素からなり、職場環境の最適化のための手法として広く認知されています。もともとは物理的な環境を整える目的で用いられましたが、今日ではデータ管理や業務の効率化にも活用されるようになり、業務のあらゆる面での最適化を目指しています。
メリット
5Sは整理・整頓を推進することで、時間の浪費が避けられるようになります。これはつまり、全体の効率化です。
たとえば、作業に使う道具を探す時間を考えてみましょう。一度にかかる時間が数十秒だったとしても、これが積み重なることで多くの時間が浪費されることになります。なお、一説によると、人は年間で約150時間を捜し物に充てているのだとか。これらの時間が5Sの実施によって短縮されれば、それは大きな生産性向上と言えるでしょう。
さらに、効率化によって作業時間が短縮されれば、従業員のワークライフバランスが向上し、これが職場の満足度と生産性のさらなる向上を促します。その他にも、5Sは社員の意識改善にも寄与します。いわゆる「割れ窓理論」(小さな問題が放置されることで、最終的には大きな問題や犯罪を引き起こす事象)で考えてみましょう。散らかった職場や放置されたゴミが、最終的には大きな事故や社員の士気の低下を引き起こすケースは少なくありません。5Sは、職場の清潔と整理が保たれ、スタッフの意識改革にも寄与するのです。
デメリット
一方で、5Sにはそれなりのデメリットも存在します。まずは活動によって複数の人々の業務時間が取られてしまう点です。また、実施後にすぐ効果が実感できるものでもないため、達成度が見えにくいという点も懸念されます。
しかし、5Sを着実に進めることは結果として生産性の向上につながります。すると、普段の業務時間自体が短縮されるため、時間に関する課題は解決に向かうでしょう。同時に、達成度や成果も見えてくるようになるため、モチベーション維持にも効果的です。
導入準備の手順
- 対象の選定:関わる場所や業務を選び、当事者意識を強めます。
- 目的・目標の設定:5Sを手段として、期待する成果を明確にします。例として、作業効率向上などの具体的な目標を設定します。
- チーム編成と役割分担:チームは5~6名程度で、役割を明確にし、チーム紹介シート、エリアマップ、チーム活動計画表などの書類を作成するのがおすすめです。
5Sそれぞれの目的と具体的な手順
次に、より具体的な5Sの内容について見ていきましょう。ここでは、それぞれの項目について「目的」を定め、その達成に向けた手順を示します。
1. 整理
目的 | 必要ないものを取り除き、必要なものだけを残す。 |
手順 |
|
2. 整頓
目的 | 必要なものをすぐに取れるような位置に整える。 |
手順 |
|
3. 清掃
目的 | 作業環境を常に清潔に保つ。 |
手順 |
|
4. 清潔
目的 | 1〜3のSを日常の状態として維持する。 |
手順 |
|
5. しつけ
目的 | 4Sを日常の習慣として根付かせ、持続的な改善を促進する。 |
手順 |
|
冷蔵・冷凍庫の温度管理でも分かる5S活動の成果
5Sで得られる成果について、冷蔵・冷凍庫を例に考えてみましょう。
まずは1と2に関わる整理整頓です。冷蔵・冷凍庫の冷房効率は、庫内の状況に左右されます。物が煩雑に詰め込まれていると、庫内が冷えにくくなるため余計に電力が必要になります。また、物を探しにくくなることもあり、扉を開ける時間が増えてさらに冷却のためのパワーが必要になってしまいます。
3の清掃についても同様です。冷蔵庫のフィルターは定期的なお手入れが必要です。詰まりなどが発生すると、明らかに温度が上昇します。同じく余計な電力消費につながるので注意しなくてはなりません。
その他、4の清潔における「維持状態の確認」も重要な要素です。たとえば、庫内の温度をチェックした際に異常が見つかったのであれば、その時点で改善処置を行う必要があります。これを一時的なものだとして放置すると故障の原因になり得ます。つまり、5のしつけが行われていることも重要なのです。
ざっとご紹介したとおり、冷蔵庫だけを例にしても5Sを行うことによる成果は大きく、未実施によるリスクは小さくありません。
庫内温度のリアルタイム監視なら「ACALA MESH」
今回は5Sに関する解説ですが、この活動をより効率的に進めるためには、システム導入などもおすすめです。
当社がご提供する自動温度管理システム「ACALA MESH」は、冷蔵・冷凍庫等の温度をリアルタイムで監視します。また、蓄積したデータを基にした作業改善などにも有用です。
たとえば、整理整頓や清掃の工程で冷蔵・冷凍庫の扉が長く開けられた状態が続くと、庫内の温度が上昇します。これは一見仕方がないことにも思えますが、データが出揃うことで改善が可能になるのです。
具体的には、清掃を行うタイミングや頻度を変更することで、庫内温度の上昇を押さえる、といったプランも立案できるでしょう。また、季節ごとに庫内温度の設定を見直すなどの施策も行えます。
このように、温度管理・記録の自動化は設備の適切な活用に役立つものです。5Sとも決して無関係ではありません。ぜひこの機会に、温度管理・記録についてもしっかりと向き合ってみてください。
まとめ
5S自体はほぼすべての食品事業者が知っている、といっても過言ではないほど有名な取り組みです。しかし、実際には取り組みがおざなりになっているところも少なくはありません。今回ご紹介した内容を踏まえて、ぜひもう一度、5Sの徹底を目指してみましょう。

