
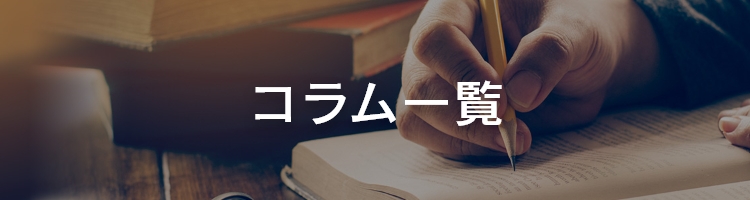
食品工場におけるDXのメリットと活用事例を紹介
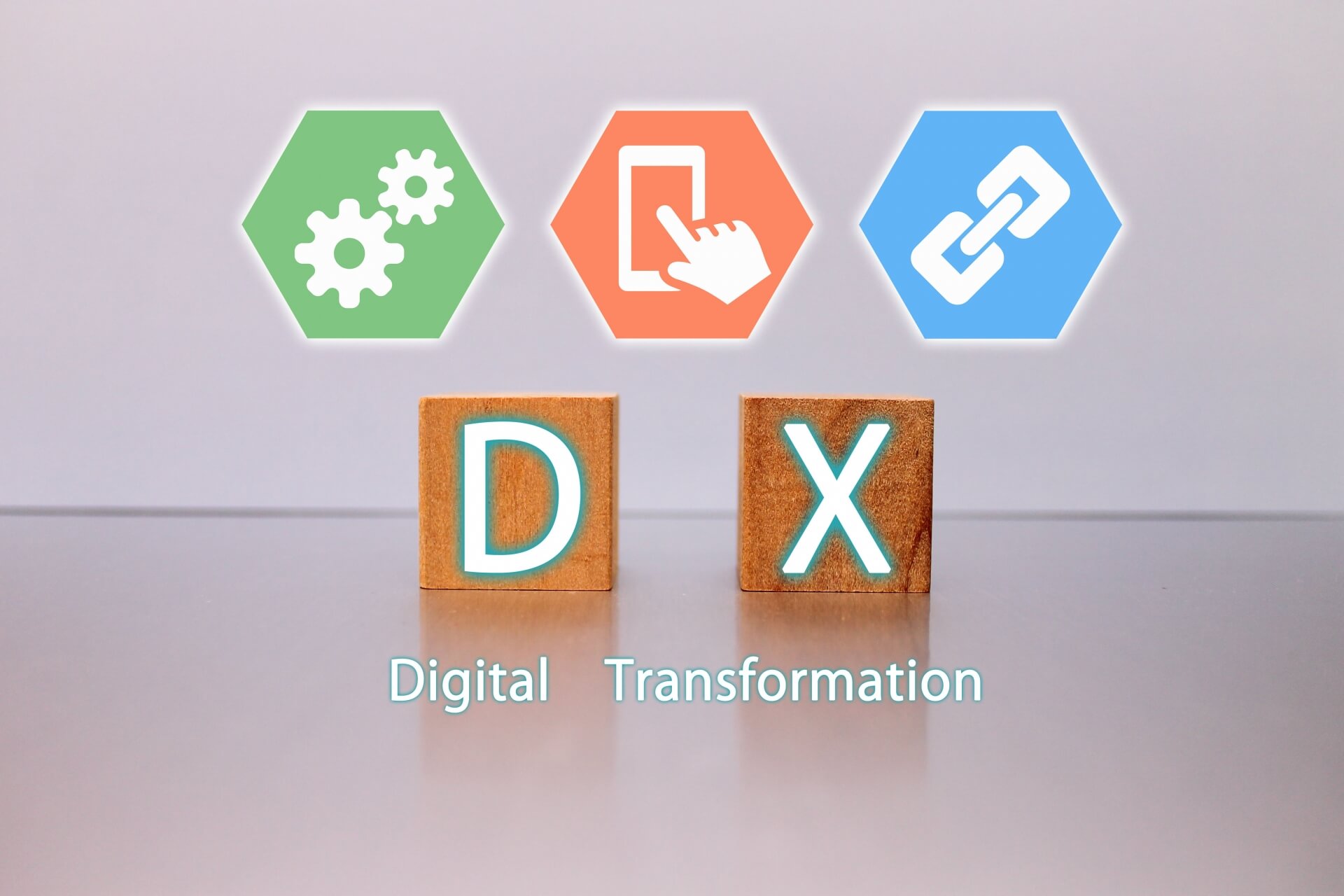
さまざまな業界で取り組まれているDX。食品工場でも、DXの推進により数多くの課題が解決することが期待されています。本記事では、食品業界におけるDX推進の現状を確認するとともに、食品工場でDXを導入するメリットと、DXにより食品工場で課題解決に成功した事例を紹介します。
食品業界におけるDX推進状況
DX(デジタルトランスフォーメーション)とは、AIやIoTなどのデジタル技術やビッグデータを活用して業務、組織、製品、サービスなどを変革し、市場における競争の優位性を確保する取り組みのことです。
食品業界におけるDXは、デジタル技術やデータの活用を通じて人手不足や食品ロスなどの課題を解決し、仕事の生産性や製品品質を向上させて、新たな付加価値の創出を目指す取り組みといえます。
富士電機は2023年、食品工場に勤務している者を対象に「食品工場におけるDXに関する意識調査」を行いました。その調査によると、75.9%が食品工場におけるDXの重要性を感じているものの、すでにDXに取り組んでいる企業は38.0%にとどまっていました。
同社による2021年の調査では、DXに取り組んでいると回答した企業は13.6%であったため、食品工場でのDXが進んでいることが分かります。しかし、食品工場におけるDXが重要と感じている企業の半数が、まだDXに取り組めていない状況が浮き彫りになっています。
参考:
食品工場でDXを進めるメリット
DXの推進により、食品工場が抱える課題が解決できる可能性があります。ここからは、食品工場でDXを進めるメリットを5つ紹介します。
業務の効率化
食品工場にDXを導入すると製造現場の一貫管理が可能になり、現場と生産管理の連携が強化されます。
DXを進めると、工場内に散らばっていた情報を一カ所に集めて管理できるようになります。手間のかかる在庫管理も、DXを導入すれば現在庫の把握だけではなく、予測まで容易になるでしょう。その他の管理すべきデータについても、自動計測システムの導入により、手書きでの記録やExcel入力の手間を省けるようになります。
また、これまで現場に足を運ばないと分からなかった事柄も、DXにより遠隔での把握・管理が可能になります。製造現場の一貫管理により判明した無駄な工程を削減すれば、業務の効率化につながるでしょう。
製品品質の向上
製品やサービスの品質を高め、顧客満足度を向上させることにもDXが役立ちます。
製造工程のデジタル管理により、原料の配合ミスや温度の調整ミスの防止、賞味期限管理の徹底などが実現されると、不良品の発生率が低下します。また、製造や検品にAIを搭載したロボットを導入すると精度の高い作業が可能になり、不良品の発生や見逃しを防げるようになるでしょう。
さらに、DXは「サプライチェーンマネジメント」の最適化にも貢献します。サプライチェーンとは、原料の調達から消費者への販売に至るまでのつながりのことです。安全な製品を消費者に届け、需要と供給のバランスをとるためにこのつながりを管理することを、サプライチェーンマネジメントと呼びます。
食品業界もグローバル化が進んでおり、サプライチェーンの把握が困難になっているのが現状です。しかしDXを活用すれば、サプライチェーンの管理も容易になるでしょう。安心安全な食を消費者へ確実に届けるため、DXによりサプライチェーンマネジメントの最適化に努めましょう。
人的ミスの削減
食品工場でDXを進めれば、人の手による作業では防げなかった人的ミスを削減できます。
近年は、デジタル技術による「スマートファクトリー化」が注目されています。スマートファクトリーとは、一貫管理により集約されたデータをもとに、現場をマネジメントする工場のことです。工場のあらゆるデータを分析することで課題を明確にし、工数削減や業務改善につなげることがスマートファクトリーの狙いです。
DXによりスマートファクトリー化が実現すれば、生産工程の見直しにより業務改善が図られて、人的ミスが削減されます。製品の品質が高い水準で保たれるため、クレームの減少はもちろん、顧客満足の向上にもつながるでしょう。
人手不足の解消
食品業界はもちろん、あらゆる業界で課題とされている人手不足も、DX化が解決を助けます。
製造工程にAIを搭載したロボットを導入すれば、高いレベルでの人の手によらない作業が可能になります。受発注業務、データの入力と集計、レポート作成などの事務作業をDXにより自動化すると、少人数でも業務を回せるようになるでしょう。
DX化による工場の一貫管理は、人手不足の解消にも役立ちます。人が工場に立ち入らなくても状況を把握できるため、少ない人員で現場を管理できます。さらに、緊急事態が発生した場合も迅速に原因が究明でき、最小限の人員での対応が可能になるでしょう。
食品ロス対策
食品業界の大きな課題とされる食品ロスも、DX化により改善が見込めます。
DXによる工場の一貫管理により、生産・販売・在庫をまとめて調整できるようになります。併せて、過去の販売数などのデータを蓄積したAIで需要を予測すれば、適正な在庫数を維持できるため、過剰仕入れによる食品ロスを防げるでしょう。
また、スマートファクトリー化も食品ロス削減に貢献します。スマートファクトリー化により製造工程が見直されると、不良品の発生が抑えられます。在庫の正確な把握により先入れ先出しが徹底されれば、賞味期限切れによる食品の廃棄もなくなるでしょう。
食品工場のDX活用事例
ここからは、実際の食品工場でDXを導入した成功事例を紹介します。
マルハニチロ株式会社
マルハニチロ株式会社は、漁業・養殖、水産物の輸出入・加工、冷凍食品などの製造・販売などの事業を展開している企業です。同社の食品工場は、取引先から求められる品質水準が高まる一方で、工場の管理業務が紙やホワイトボード、Excelなどを使用した手作業で行われていることが課題でした。
そこで同社は、生産管理システムの導入による食品工場のスマートファクトリー化を決定します。同社は全国に展開する7つの工場のデータを一貫管理し、それぞれの工場で異なっていた業務プロセスを標準化しました。その結果、在庫回転率が2倍に向上し、在庫の滞留期間を短縮できました。
そのほか、配合ミスや計量ミスの減少、業務効率化による人的負担の軽減にも成功。ある工場で、出力していた紙の帳票の枚数が4分の1になったことも成果の一つです。また、ミスを未然に防ぐ仕組みの構築にもDXが役立っています。
株式会社山神
株式会社山神は、ほたての養殖・加工・販売事業を展開している企業です。HACCP認定を取得し、製品の安全性と品質の高さをアピールしています。
しかし、20以上ある冷凍庫と冷蔵庫の温度を1時間ごとにチェックし、温度をノートに記載する作業に毎日2~3時間費やしていました。この温度チェックは従業員にとってかなりの負担になっており、温度確認やノートへの記載が漏れることもありました。
そこで同社は、温度自動計測システムである「ACALA MESH」を導入。冷凍庫と冷蔵庫に取り付けたセンサーにより、温度計測とパソコンへのデータ送信が自動で行われます。その結果、温度をチェックしてノートに記載し、パソコンに入力する手間が削減されました。
また「ACALA MESH」では、外出先でもデジタルデバイスで工場内の冷凍・冷蔵庫の温度を確認できます。さらに、温度や湿度が基準値を超えるとアラートで通知するため、異常時の迅速な対応が可能です。同社は「ACALA MESH」の導入により業務が効率化され、従業員は本来の作業に専念できるようになりました。
まとめ
食品工場におけるDXは、重要性の認識が広がっているものの、実際のDX化はあまり順調に進んでいないのが現状です。しかし、人手不足や食品ロスなどの課題を数多く抱える食品工場こそ、DXを進めるべき現場といえます。
DXの導入を「ACALA MESH」から始めてみませんか? 「ACALA MESH」を利用すると、食品工場の業務に欠かせない温度・湿度管理が自動化されます。煩雑な設定は必要なく、センサーやベースステーションを設置し、簡単な初期設定だけですぐに利用開始できます。IT知識がなくても容易に導入できるため、DX化のスタートに「ACALA MESH」の利用を検討してみてください。

