
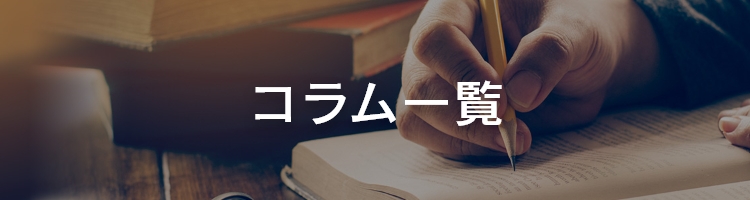
食品工場におけるエネルギー設備の特徴と省エネポイント
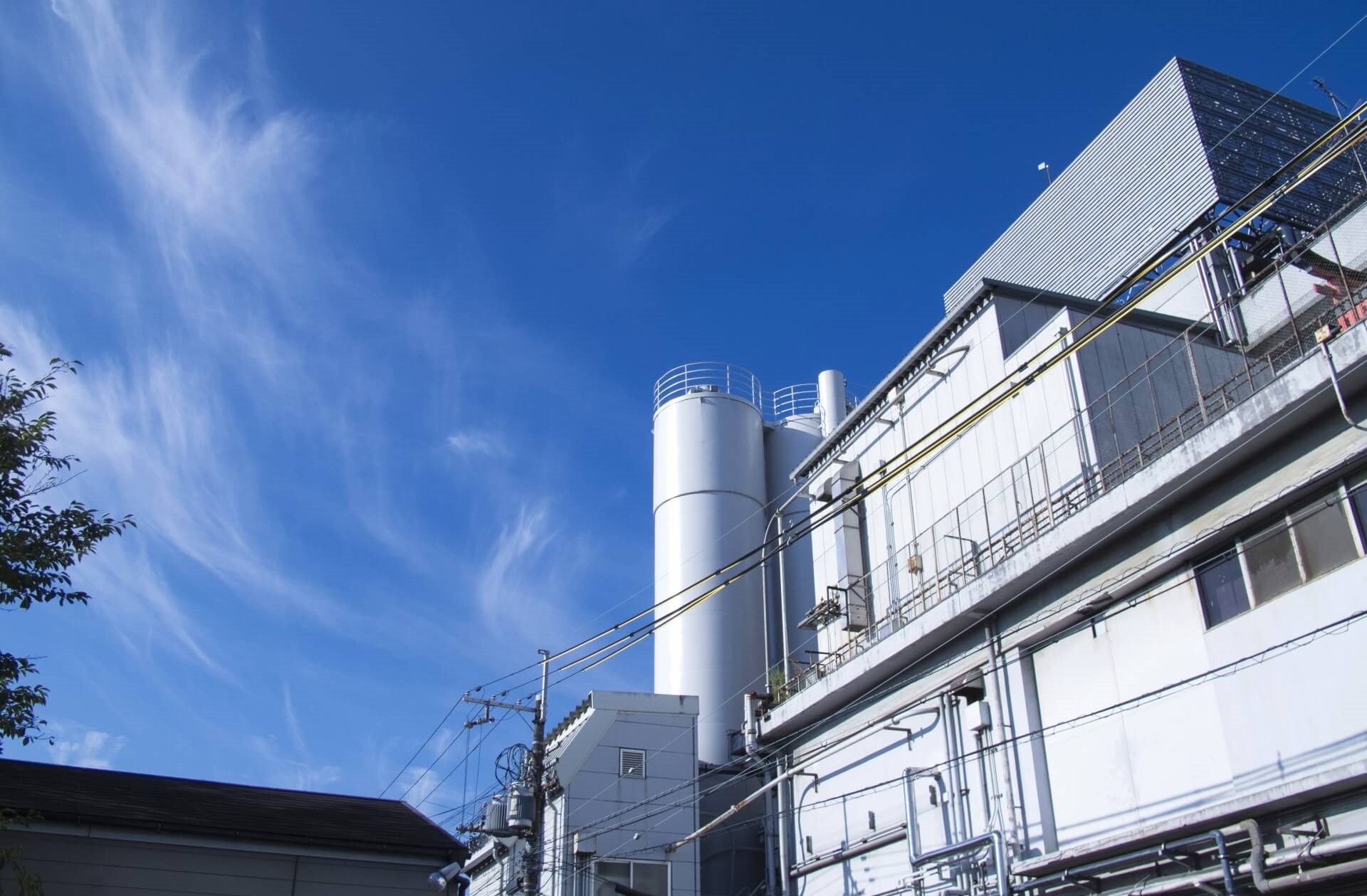
食品工場を運用する上で避けては通れないコストの問題。今回はそのなかでも、エネルギー設備とそれに関わる省エネポイントについて解説します。
食品工場の主なエネルギー設備
まずは食品工場における主なエネルギー設備を簡単にご紹介します。
空調・換気設備
空調・換気設備は食品工場内の温度・湿度を一定に保ち、食品の品質劣化を防ぐとともに、従業員の快適な作業環境を維持する重要な設備です。厚生労働省の大量調理施設衛生管理マニュアルでは、高温多湿を避け、温度25℃以下、湿度80%以下に保つことが望ましいとされています。
冷凍・冷蔵設備
冷凍・冷蔵設備は、原料や製品を適切な温度で保管するための重要な設備です。具体的には冷凍・冷蔵倉庫や急速冷凍機、ショーケースなどが挙げられます。食品衛生法では温度管理が義務付けられており、適切な対策が求められます。
ボイラー・加熱設備
食品の加熱殺菌や調理、洗浄などに使用されるボイラー・加熱設備は、食品工場で欠かせない設備のひとつです。安定した蒸気供給が求められるため、機器の定期的なメンテナンスが必要です。
コンプレッサー・ポンプ類
製造ラインの駆動源や工場設備の動力源になるコンプレッサー・ポンプ類。圧縮空気の供給や冷却水の循環などに不可欠な設備であり、食品工場においても適切な使用が求められます。
照明設備
照明設備は、作業環境の安全性確保に不可欠な設備。衛生管理の観点から防水・防塵性能や清掃のしやすさも求められます。
エネルギー設備のコスト削減ポイント
上記で挙げた設備のコスト削減につながるポイントをご紹介します。
空調・換気設備の省エネポイント
空調・換気設備の省エネを実現するためのポイントとして、まずフィルターの定期的な清掃や交換が挙げられます。フィルターが目詰まりすると風量が低下し、効率が悪化するため、定期的なメンテナンスが必要です。また、適正な温度設定も重要です。夏季は28℃、冬季は20℃に設定することで、1℃の変更ごとに約10%の省エネ効果が見込めます。これにより、無駄なエネルギー消費を防ぎます。
さらに、高効率機器への更新も効果的です。高効率の空調機やヒートポンプ式空調の導入により、30%以上の省エネを実現した事例もあります。最新の省エネ技術を採用することで、大幅なエネルギー削減が期待できます。
これらの取り組みを総合的に実施することで、空調・換気設備の効率を最大限に高め、環境負荷を低減できます。
冷凍・冷蔵設備の省エネポイント
まず、設定温度を見直し、食品に適した温度を設定して過剰な冷却を避けることが大切です。そのためには、食材を必要な温度帯ごとに分け、リアルタイムに監視できる体制の構築も求められます。
冷凍・冷蔵設備のドアの開閉時間を最小限に抑えることで、庫内温度の上昇を防ぎ、エネルギー消費を削減する取り組みも重要です。マニュアルの整備はもちろん、どのように設備が利用されているかのデータを記録・分析することで改善ができる場合があります。
その他、インバータ制御や自然冷媒を用いた最新の高効率冷凍・冷蔵機器への更新、IoTを活用した自動温度計測・記録・監視システムの導入による温度管理の自動化と省力化、人為的ミスの防止もおすすめの取り組みです。
これらの取り組みを総合的に行うことで、冷凍・冷蔵設備の省エネ効果を最大限に引き出せます。
ボイラー・加熱設備の省エネポイント
ボイラー・加熱設備の省エネには、燃焼効率の改善と排熱回収が重要なポイントとなります。燃焼効率の改善では、まず空気比を適正化することが求められます。これにより、燃料の完全燃焼が促進され、未燃焼ガスの排出が減少し、燃料の無駄を削減できます。また、運転管理の最適化も重要です。定期的なメンテナンスとリアルタイムの監視を通じて、ボイラーの性能を常に最適な状態に保てます。そのためには、燃焼状態のモニタリングや自動制御システムの導入がおすすめです。
次に、排熱回収の取り組みです。排ガス中に含まれる高熱を、エコノマイザーを通じて回収し、給水を予熱することで、エネルギー効率を大幅に向上できます。これにより、ボイラーが新たに必要とする熱エネルギーの量が減り、燃料消費量を抑制できます。さらに、排熱回収システムを導入することで、全体のエネルギー使用量を最適化し、運用コストの削減にもつながります。
コンプレッサー・ポンプ類の省エネポイント
コンプレッサー・ポンプ類の省エネを実現するためには、インバータ制御の導入が重要です。インバータ制御は、負荷に応じた回転数制御を行い、必要なエネルギーだけを消費するため、無駄なエネルギー消費を削減します。これにより、運転効率が向上し、エネルギーコストの削減が可能となります。
台数制御も効果的な省エネ対策です。複数のコンプレッサーやポンプを効率的に運用することで、部分負荷時の効率低下を防ぎ、最適な運転状態を維持します。例えば、需要が少ない時には一部の機器を停止し、需要が増加した際には必要に応じて追加の機器を稼働させることで、全体のエネルギー消費を最小限に抑えます。
照明設備の省エネポイント
照明設備はLED化が省エネにつながります。長寿命で高効率なLED照明を導入することで、従来の照明に比べて40%以上の省エネが可能です。
人感センサーの導入も効果的です。人の存在を検知して自動的に点灯・消灯することで、無駄な点灯を防ぎ、エネルギーの消費を抑えます。また、照度の見直しも重要です。過剰な明るさを抑え、必要十分な照度に調整することで、さらに省エネ効果を高めることができます。
その他の省エネ・脱炭素対策
前項でご紹介した以外にも、工場における省エネ対策の方法はいくつも存在します。また、脱炭素に向けた取り組みについていくつかご紹介します。
温度管理はコストカットのファーストステップ
食品工場において、温度管理の適切な実施は大きなコストカットにつながります。温度を適切に管理することで、エネルギー消費を削減し、冷凍・冷蔵庫の効率を最適化できます。また、食品の品質を保つことで廃棄を減らし、食材のロスを最小限に抑えます。さらに、温度管理は食品安全性の確保にも不可欠であり、リコールやクレーム対応のコストも削減できます。
しかし、人力による温度管理は非効率であり、精度も高くありません。そこでおすすめするのが、当社がご提供する自動温度管理システムACALAです。ACALAはIoT技術を活用し、リアルタイムで温度を監視・蓄積するため、精度の高い設備管理が可能です。1分毎のデータを見える化できるため、フィルターの目詰まりやドアパッキンの劣化など、人力では検知が遅れる設備の不具合も迅速に検知可能です。見える化したデータを活用して、例えば、最適なタイミングで機器メンテナンスを行うことで、大幅な省エネ効果に繋がります。HACCPで義務化されている温度記録は、この自動化されたシステムにより、人的ミスを防ぎ、効率的な運用が実現でき、食品安全基準を確実に満たすことができます。このように温度管理システムの導入は、エネルギーコストの削減、廃棄の最小化、安全性の向上を同時に達成し、食品工場全体のコストを大幅に削減することに貢献します。
バイオマス・バイオガス利用
バイオマスとバイオガスの利用は、化石燃料の使用を削減し、二酸化炭素排出量低減につながります。食品廃棄物を燃焼して得られるバイオマスエネルギーや、嫌気性消化で生成されるバイオガスは、工場の加熱プロセスや発電に利用可能です。これにより、化石燃料の使用が削減され、エネルギーコストと二酸化炭素排出量が低減されます。また、廃棄物の再利用により廃棄コストも削減でき、環境保護にもつながります。
工場の断熱性向上
断熱材や遮熱塗装を用いることで、建物の断熱性を高められます。これにより、外部の暑さや寒さが室内に影響するのを防ぎ、空調負荷が大幅に低減します。結果として、冷暖房にかかるエネルギー消費が削減され、省エネ効果が得られます。特に、夏場の冷房負荷や冬場の暖房負荷が軽減されるため、快適な室内環境を維持しながらエネルギーコストの削減が実現します。
システムでエネルギー使用量を「見える化」
エネルギーマネジメントシステム(EMS)を導入すると、電力やガスなどのエネルギー使用状況をリアルタイムで可視化できます。これにより、無駄なエネルギー消費を特定し、効率的なエネルギー管理が可能になります。また、EMSはエネルギー使用パターンの分析を通じて省エネ対策を効果的に推進し、コスト削減と環境負荷の低減を実現します。リアルタイムでの監視とデータの活用により、持続可能なエネルギー運用が可能となります。
まとめ
食品工場の省エネ施策はコストカットだけでなく、脱炭素などの環境問題に直結する取り組みです。当社では、自動温度管理システム「ACALA」を通じて、食品製造業を営むお客様に温度管理・記録ソリューションをご提供しています。温度管理・記録の自動化をご検討中のお客様は、ぜひ当社までご相談ください。

