
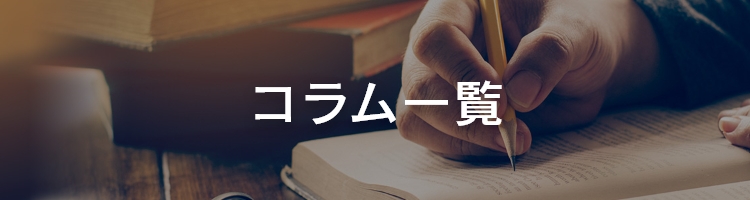
設備長持ち&効率化!予知保全と食品製造業
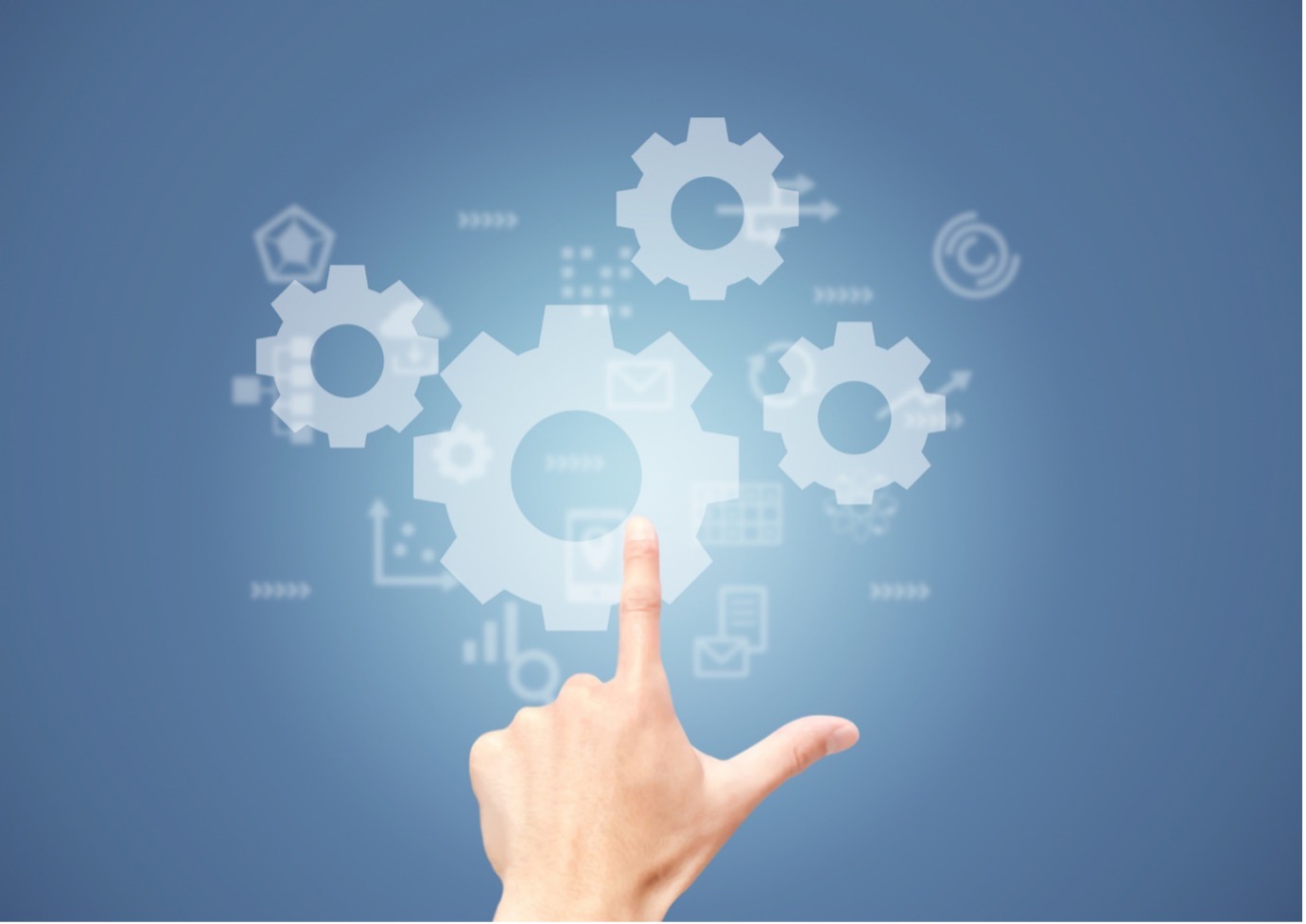
食品製造業では、さまざまな設備・機器が使われています。これらのメンテナンス方法として近年注目を集めているのが予知保全です。今回は、食品製造業における予知保全の基礎知識を解説します。
予知保全とは?
食品製造業に限らず、設備や機器等を用いる事業者にとって、予知保全は欠かせません。
まず、予兆保全の定義から先に把握しておきましょう。これは、設備や機械の状態を監視することで故障の兆しを検出し、その状況に応じたメンテナンスを行う方法を指します。監視の方法はさまざまですが、近年はIoTセンサーや高度なデータ処理技術を利用し、未発見の問題を検出できるようになってきました。従来の技術者の勘や、頻度の少ない点検では分からなかったような不具合も、テクノロジーの進歩によって高精度に検知できる時代となっています。
なお、予知保全は「予兆保全」とも呼ばれています。とくに、AIや機械学習を使用して検知を行う場合にこの名称を用いるケースが多いとされていますが、明確な定義の違いはとくにありません。
予防保全だけでは足りない?
予知保全が普及する以前までは、予防保全という方法がメンテナンスでは用いられていました。これは、「これ以上の稼働は故障につながる」とされる使用回数や時間を決め、事前に部品交換などの保全を行う方法です。具体的な数値等についてはメーカー発表があったり、技術者の経験即から予測がされたりしていました。
予防保全は突然の事故を避けるのには効果的な方法です。しかし、適切なタイミングを見極めるのが難しかったり、過剰な保全によってコストがかさんでしまったりといった問題がありました。
この課題の解決方法として、予知保全は近年注目を集めるようになりました。メンテナンスコストの削減はもちろん、以前までは検知が難しかった異常値も検出が可能となっています。
なお、予防から予知への保全方法の移行は食品製造業や工場設備だけでなく、国の重要なインフラの保全にも活用されています。経済産業省も、このパラダイムシフトの推進を検討している段階にあり、今後さらに重要度が高まると考えられています。
食品製造業における予知保全システムの導入
それでは、実際に予知保全がどれだけ食品製造業へと拡がってきているのかについても見てみましょう。富士電機による調査「食品製造業におけるIoT/ITの利用動向調査」では、「予知保全システムを既に導入している」との回答は、全体の43%にものぼりました。さらに、「今後、利用を検討している」という回答は30%です。それぞれを合算してみると、導入を前向きに捉えている事業社は全体の7割を超えており、すでに多数の事業社が予知保全システムを活用していることが分かります。
予知保全の効果と活用
次に、予知保全によって得られる効果や、活用のポイントについても見ていきましょう。
ダウンタイムの低減と生産性向上
予知保全は故障の予兆を捉えることで、突発的な設備停止を防ぎます。設備・機器の故障は、予期せぬダウンタイムとその生産活動へ大きな影響を与えます。故障した設備次第では、そもそも製造自体をストップせざるを得ない状況もあり得るのです。
予知保全によって故障の前兆を把握できれば、代替機の手配や、生産を行っていないタイミングでの検査・メンテナンスなどが実施可能となります。結果、事業が被る被害を最小限に抑えられるのです。
効率的なメンテナンスと人件費の削減
IoTを組み込んだ予知保全システムは、より効率的なメンテナンス作業に寄与します。
機器のメンテナンスには人手が必要です。しかし、IoTによって故障箇所や原因の特定が済んでいれば、それだけでかなりのリソースを節約できるでしょう。さらに、遠隔作業支援システムなどを併用すれば、より正確かつ重要な指示を、場所を選ばずにメンテナンススタッフが現場へと届けられるようになります。
こうした取り組みは、人件費の削減にも直結します。従来であれば多くのスタッフや外部パートナーを巻き込むようなメンテンナスでも、現在は最少人数かつ最少工数での対応が実現できるのです。
保全作業のデータ化と属人化脱却
予知保全はAIやデータ分析を活用し、熟練作業者のノウハウに依存することなく、一貫した保全判断が可能となります。設備の故障について、ベテランスタッフによる指摘がなければ気づけないような状況はリスキーです。属人的な判断ではなく、誰にでも故障の兆候が発見できるよう環境を整えられる必要があります。
また、上記を実現することは教育コストを下げ、新人でも効果的な保全活動を実施することにつながります。結果として、人件費の削減につながるケースもあるでしょう。
設備の総コスト削減と長寿命化
状態ベースでの保全活動は、不要な部品の交換や過剰なメンテナンスを避け、設備のライフサイクルコストを削減し、同時に設備の寿命を延ばすことができます。
また、不調があるにも関わらず使用を続けるような状況には注意が必要です。たとえば冷蔵庫の場合、冷却能力が低下しているのに使用を続けると、余分な電力消費となるため、経済的にもエコロジー的にもマイナスです。
不調が出た時点で整備を行い、高いパフォーマンスを維持することは、地球環境保護にもつながる重要な視点です。SDGsが叫ばれる昨今においても、予知保全は欠かせない要素と言えるでしょう。
【事例】コンビニエンスストアやスーパーマーケットの冷蔵ショーケース
より具体的な事例についても考えていきましょう。例として、コンビニやスーパーの冷蔵ショーケースで解説します。
冷凍ショーケースの故障は、小売店にとって大きな損失につながります。適切な温度を維持できない冷凍ショーケースに商品は陳列できないので、当然販売機会が失われます。一時的なメンテナンスであったとしても、決して少なくないダメージとなるでしょう。
もう1点はより重要な要素です。たとえば、冷凍ショーケースの故障に気付くのが遅れてしまった場合を想定してみましょう。この場合、指定の温度帯以上に商品がさらされている可能性が高く、場合によっては商品の回収に発展する可能性もあります。
さらに言えば、温度管理ができていなかったことで食中毒などが発生してしまった場合は、より大事です。被害に遭われた方への賠償だけでなく、今後は企業の信頼度回復といった長い道のりが待っています。
冷蔵庫の予知保全におすすめ「ACALA MESH」
前項のような冷蔵・冷凍庫の予知保全には、当社がご提供する「ACALA MESH」が適任です。
冷蔵・冷凍庫は完全に故障する前に、一時的な温度逸脱が増えるといった傾向があります。また、平均温度の上昇なども、冷却能力低下の兆候と言えるでしょう。
「ACALA MESH」は、設置した温度ロガーの計測データが分単位でクラウドサーバーへと送信されます。蓄積された膨大な量のデータ管理とリアルタイム監視によって、故障の予兆にもすばやく気付くことができます。
今後、冷蔵・冷凍庫の予知保全に取り組んでいきたいとお考えであれば、ぜひ「ACALA MESH」の導入をご検討ください。
まとめ
予知保全は設備・機器の適切なメンテナンスにつながり、寿命の延長にもつながります。リスクの回避だけでなく、直近のコストにも関わってくるのです。
さらに、予知保全のために取得していたデータは、今後の作業効率化にも必ず役立ちます。食品製造を安心・安全、かつスピーディーに行うためにも、ぜひ前向きに取り組んでいきましょう。

